DM Glassware is a glassware manufacturer in China
We are producing various kinds glass drinkwares by machine. We also offer services of glassware decorations, including logo decal application, painting, engraving, printing, etc.
Our main products are machine-made glasswares, glass cups, glass drinkwares and tablewares for home and kitchen use. Such glasses like glass tumblers, glass mugs, whiskey glasses, shot glasses, glass candy jars, glass bowls, beer glasses, etc.
We are well-equipped with advanced machines with annual output is around 1 million tons of high-grade glasswares. The daily output of 950,000 pcs glasses, our 700 employees and 150 professional technicians make DM a great team.
- Fast Production & Delivery – We are keeping on developing new mouldings to increase the market occupation. Continuing productions ensure fast turnaround time.
- Customization – Our customization process is strictly supervised by our production protocols. We can produce glasswares in specific designs, shapes, sizes, etc.
- Decoration Options – DM Glassware offer different options of decoration, like decals, laser, etching, painting, and other necessary accessories.
- Internal Inspection – Our QC team will do internal inspection for every piece of order, during production. This is to avoid any mistakes before they go bigger.
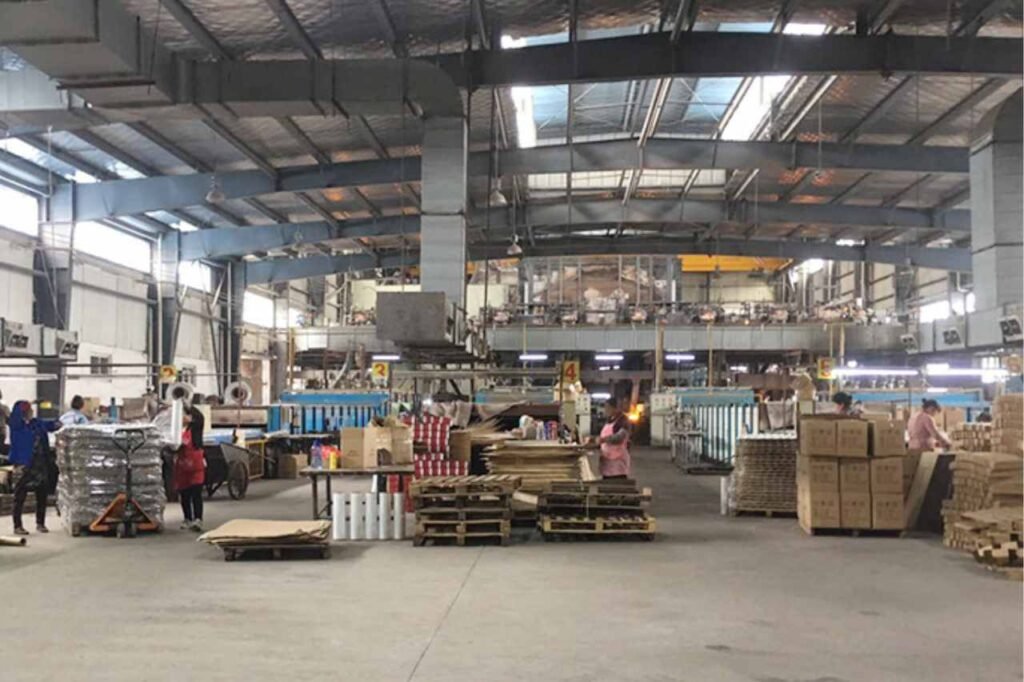
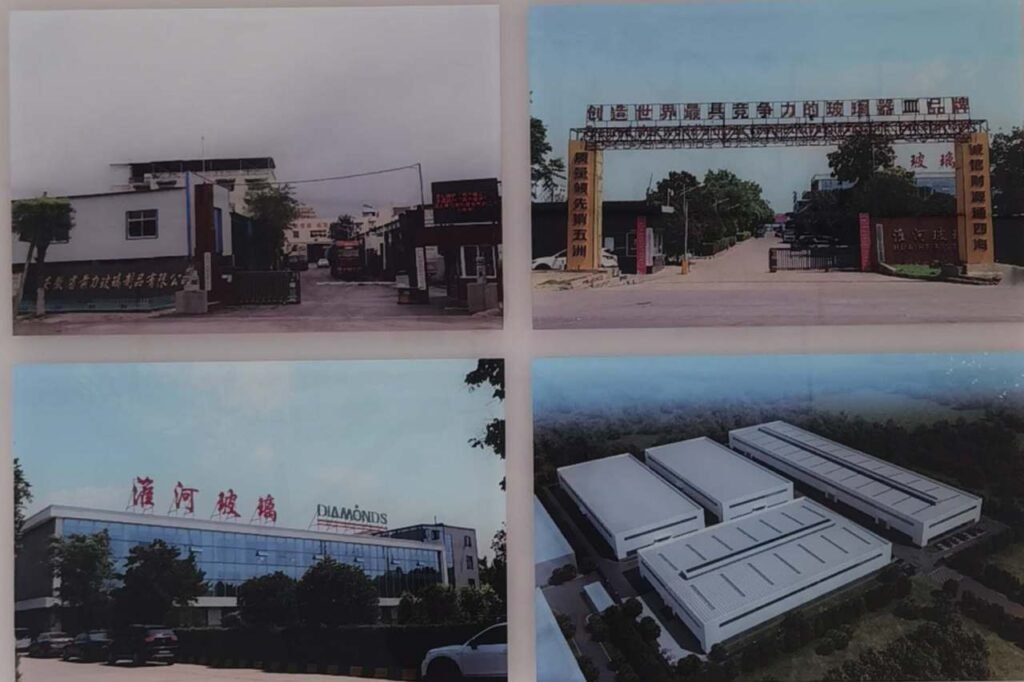
Why Choose DM
Factory Direct Supply
We are a professional glassware manufacturer, supplying products directly from our factory with competitive pricing and consistent quality for bulk orders.
High-Quality Materials
All our glassware is crafted using food-safe, durable, and eco-friendly materials. This guarantees reliability and safety for your end customers.
Custom Design Options
We provide a wide range of customization services, including logo printing, engraving, and painting, helping you create unique glassware that aligns with your brand.
Global Shipping Capability
With experience in exporting worldwide, we ensure secure packaging and timely delivery to meet your business schedules, no matter your location. You have no worries.
Advanced Production Lines
Our state-of-the-art facility features 5 advanced production lines and modern kilns, allowing us to meet large-scale orders efficiently without compromising quality.
Trusted B2B Partner
With years of experience serving wholesalers, distributors, and retailers, we understand the needs of B2B buyers and deliver tailored solutions to grow your business.
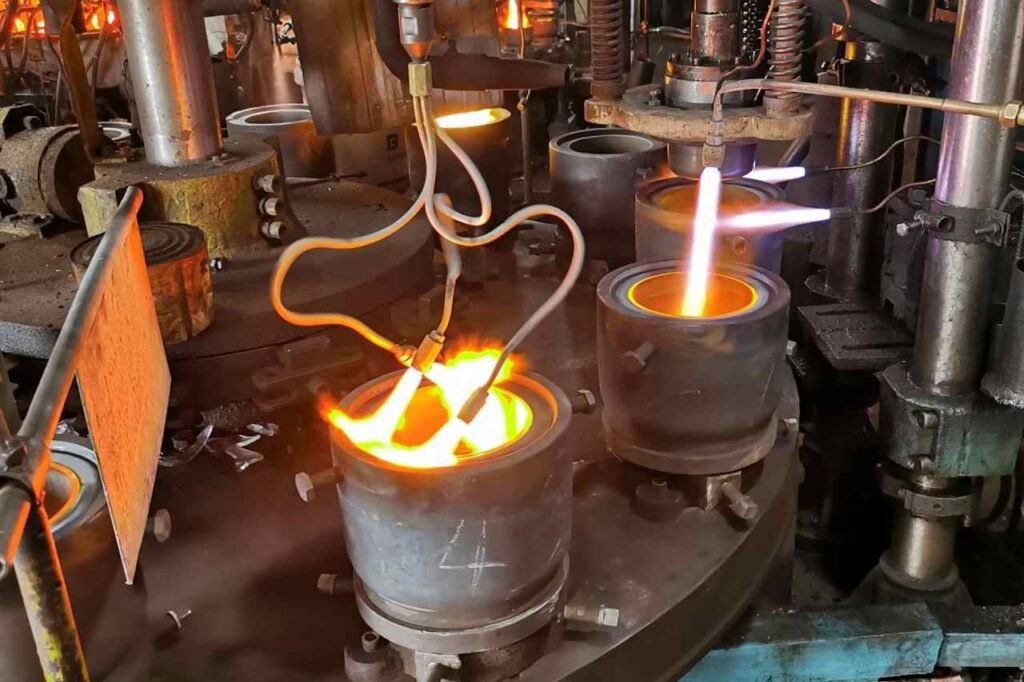
Qualified Glassware Manufacturing
DM Glassware is an expert when it comes to glassware manufacturing. We use soda lime glass as the main raw material. With advanced equipments and techniques, millions of glass cups are produced in shiny bright clear, like diamonds.
Various types of glasswares are in high quality. They also can be customized to meet your specific requirements.
DM Glassware Factory Certification
DM Glassware is a certified company of machine-made glasswares.
Many Products & Technology Patents are approved we can provide qualified glass products and servives at the competitive costs.
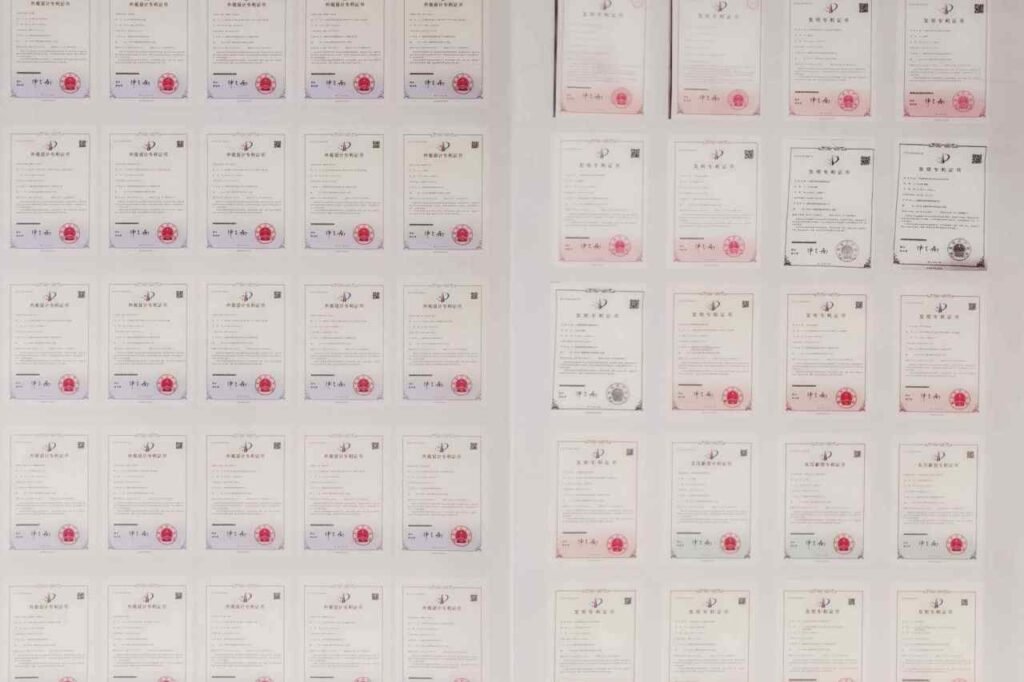
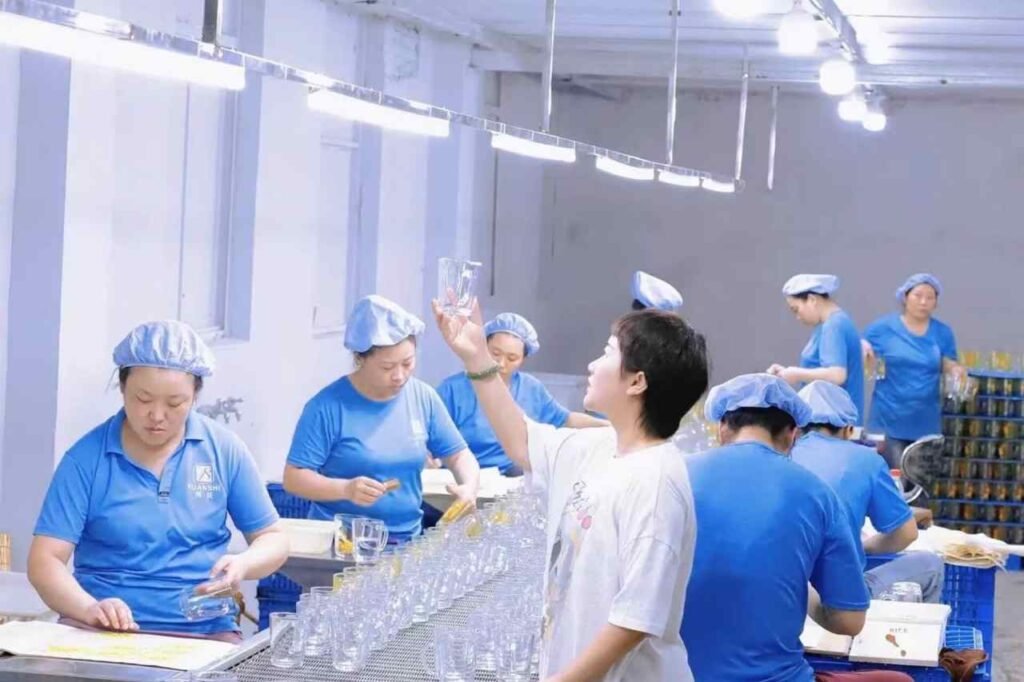
DM Glassware Quality Control
We offer the service of internal inspection during mass production. It is an important step to ensure the quality.
From raw material to the final completed glass cup, every step must be ensured to go on right.
What is The Glassware Manufacturing Process?
You must be interested in how a glass cup has been produced from just Sio2 sands.
Here you will see the full process of glassware manufacturing.
Table of Contents
Raw Materials Of Glasswares
The main raw materials for making glasses are silica sand, sodium carbonate, limestone and other auxiliary materials. Normally we will say our glassware material is soda lime glass.
Silica Sand
Silica sand is the basic raw material for making glasses, occupying more than 70% of the raw materials of the whole glass. Silica sand is a mineral mainly composed of silica, with high temperature resistance and chemical stability, not easy to be eroded by chemicals, while silica sand is cheaper, is the ideal raw material for glass production.
Sodium Carbonate
Sodium carbonate is the main alkaline oxidizer for glass. Under high temperature conditions, sodium carbonate can dissolve silica sand, prompting the formation of liquid glass materials. During the sintering process, sodium carbonate can also reduce the number of bubbles in the glass and improve the transparency and quality of the glass.
Limestone
Limestone is mainly used as a degassing agent for glass. In the production process of glass, adding the right amount of limestone can absorb and remove oxygen, carbon dioxide and other gases, preventing bubbles inside the glass. At the same time, in the production process of glass, limestone can also improve the hardness and wear resistance of the glass.
Other Auxiliary Materials
In addition to the above main raw materials, the production of glass also need to add other auxiliary materials, mainly including sandy auxiliary materials, oxidizing agents, coloring agents and so on. These auxiliary materials can change the color, texture and transparency of the glass and other physical properties, but also to improve the impact resistance and heat resistance of the glass.
DM Glassware Raw Material Workshop
Molds For Glassware Manufacturing
To produce different shapes and forms of glasses, we need to design and make molds. Therefore, the quality of glass products is closely related to the material, structure, processing accuracy and maintenance of the molds.
Let’s take machine pressing glass as an example here. The characteristics of pressing molds are that the punch determines the inner shape of glass products and the inner cavity of the mold determines their shape.
We routinely use the mold material is cast iron, its casting performance is very good, low cost, hot and non-stick, is the most cost-effective one. At present, many of our customers require customized on said cast iron mold.
According to our disc machine operating table, it is needed to be equipped with 24 pairs of molds, 3 pairs of punches, 3 pairs of lids. This set of molds can probably produce 50-80 million glasses. The mold is processed by CNC machining process, which must ensure the precision and quality of the mold. After the mold is processed, it needs to be heat-treated, including quenching, tempering, etc., to improve the hardness and abrasion resistance of the mold.
Glassware Molds
Before formal production, we need to install the mold to do trial production, replace the mold about 2-3 hours after the finished glass is considered stable. Our inspection team will supervise all the process till the glasses are finished. It is very necessary to ensure the qualified production.
The Specific Glassware Manufacturing Process
Melting of Glass Raw Materials
The raw materials are the above mentioned, but each factory’s formula ratio is different. It makes every piece of glass cup the unique one. For example, the transparent color differs so much. One might be super white and clear while the other one is foggy and seems grey. As an expert in this area, we often know the manufacturer of one glass by its glass color and surface.
Workers will put a certain proportion of the configuration of the raw materials, which will also add a portion of broken glass, into a large high-temperature glass melting furnace for melting. In this process, the temperature of the furnace and the melting time need to be controlled to ensure that the glass raw materials are completely melted and the various components are evenly distributed.
Glass Melting Furnace
Glass Molding
When the material melting is completed, it will reach the cutting mouth through the downstream channel.
Cutting Mouth Tunnel
Then the melting glass material will be directly dropped into the inner cavity of the mold, with the punch pressing, the glass cup will be initially shaped. When the glass material falls into the mold, the turntable keeps rotating. One mold after another will be turned to the exact place of downstream tunnel.
Production Plateform
The production plateform will be fixed with one or several gas lances to keep the mold stay hot. The spray gun can be sintered in 360 degrees, so as to achieve the purpose of smoothness and no burr.
Fire Gun For Glassware Polishing
Annealing Process
After the polishing process, the robot takes the glass cup out, puts it on a conveyor belt. They will enter into a long annealing kiln, a process that prevents rapid cooling from breaking the glass surface or creating cracks. This slow cooling and annealing removes stress, improves stability and strength, and ensures the quality of the glass cup products.
Annealing Furnance
Quality Inspection of Finished Glassware
When the glass passes through the annealing furnace, it comes to the quality inspection platform. In every production line, 3-4 people will be arranged to inspect the glass products as well as packing.
Here is the video for glassware manufacturing process, which helps you to understand.
Possible Glassware Quality Problems
- Bubbles: Bubbles appear on the wall or the bottom of the glass, small or big.
Solution: Mix the materials well, adjust the ratio of raw materials; stabilize the temperature and pressure of the kiln.
- Deformation: Mostly appear in the round cups with rounded mouth and deformed body.
Solution: Check the molds, replace the spare molds in time, and repair the replaced molds.
- Unknown mixture: There are white flocculent in the glass.
Solution: The material hasn’t melted completed. Better reducing the input of broken glass and make the melting completely.
- Surface roughness: Glass surface is with oil, or water ripples, or miscellaneous materials. For open-molded glasses, the seam line is very sharp.
Solution: Increase the number of gas spray guns to enhance the polishing process.
- Broken glass: Any part of the glass is damaged or broken.
Solution: Throw it to the waste collection box.
Packaging Options of Finished Glass Products
Pallet Packaging
This pallet packing option is uitable for glasswares that require secondary processing.
On the pallet, we put a piece of big paper tray on the bottom. Then the workers will put the glasses one by one neatly. When the first layer is finished, they put another big paper tray on it. Layer by layer, one pallet is suitable to set at 1m height. Then we wrap this pallet of glasses with the plastic film. This is to keep all glasses safe. The next step is the workers pull it into warehouse using a trailer.
Pallet Packaging
Carton Packaging
Some clients only require the clear glass products. Customized packaging cartons need to be prepared 15 days before the product goes online and delivered to our packaging warehouse. Once the finished products are manufactured and pass quality inspection, they can be directly packed into the cartons. The cartons are also put neatly on pallets, wrapped with stretch film, and stored in the warehouse.
Carton Packaging
During the production process, different clients have different requirements. For instance, if a client requires labels on each glass, we can arrange our automatic labeling machines to solve it. To be reminded, the client must provide the labels in advance. Alternatively, we can customize labels according to the client’s specifications.
Automatic labeling Machine
Carton Packaging Types
Carton with partition: This type is suitable for products requiring secondary packaging, serving as a transit box. The advantage over pallets is that transit boxes can significantly reduce the breakage rate of products, and the cost of the cartons is also relatively appropriate.
For small and medium-sized glassware such as shot glasses, mugs, whiskey glasses, or beer glasses, this packaging method greatly reduces procurement costs. Typically, the external cartons for foreign trade exports are made of five-layer corrugated paper, which is sturdy enough for direct container loading without risk of damage.
Mass Production Carton Packaging
Inner box plus outer carton: This method provides better protection for the glassware and essentially eliminates product damage.
For medium-sized glasses, the inner box generally holds six pieces, and the outer carton can hold eight boxes, totaling 48 pieces per carton. This packaging method keeps the gross weight of each box under 20 kilograms.
For larger sizes, such as beer glasses, a box can approximately hold up to 24 pieces. To control costs, the inner boxes are made of three-layer corrugated paper, and can be printed with customer-specific information; the outer box can also be customized with shipping marks.
6pcs Brown Inner Box
About the inner box: If a client requires that the product be sold directly in boxes, the inner boxes can be made of color box material. Because a colorful packaging box, branded with customer information, is more likely to attract consumer purchases.
Shot Glass Inner Box Packaging
Other requirements: For gift shops, you can opt for individually packaged color boxes, which is also a way to increase sales volume.
DM Customization Service
Glass cup customization refers to the process of designing and modifying glass cups to meet specific preferences or branding needs. This can include adding logos, artwork, colors, or other personalized elements. Customization allows businesses or individuals to create unique glassware that reflects their identity or message.
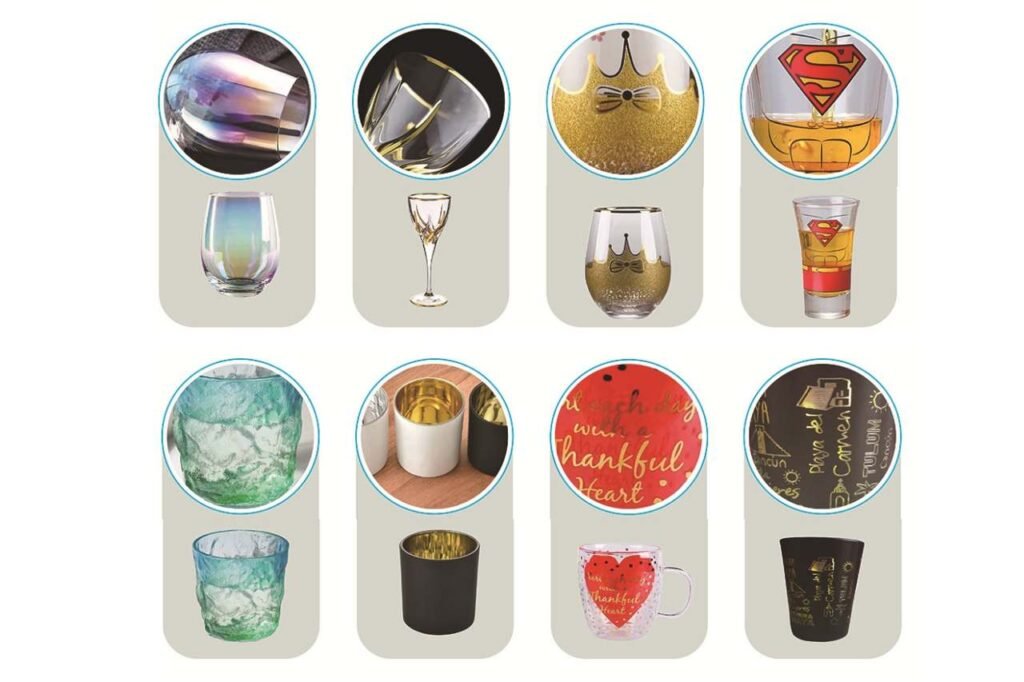
Decorations/Laser Engraving
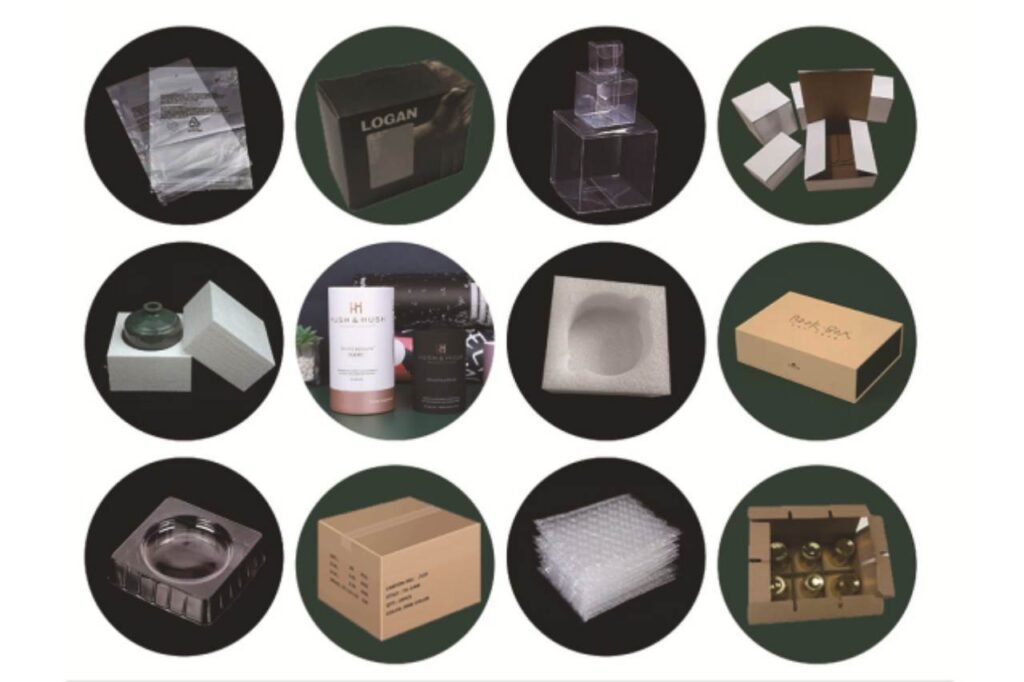
Custom Packagings
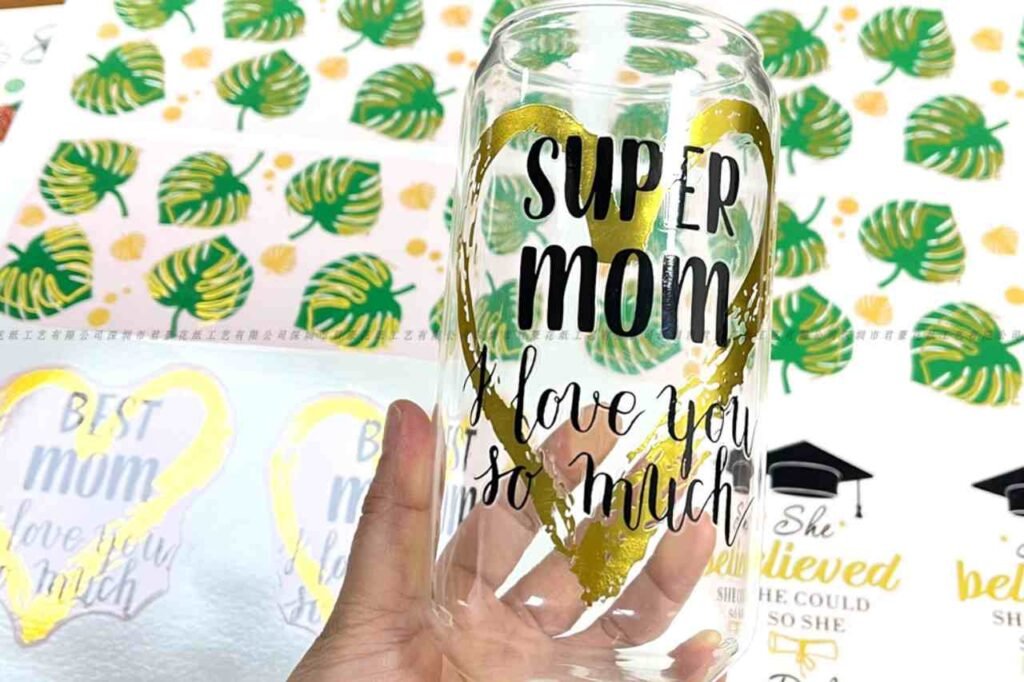
Logo Placement and Branding
Custom glass cups can be designed with logos and branding elements placed strategically for maximum visibility. The logo can be printed on the side, base, or even wrapped around the glass.
The regular option is using decals.
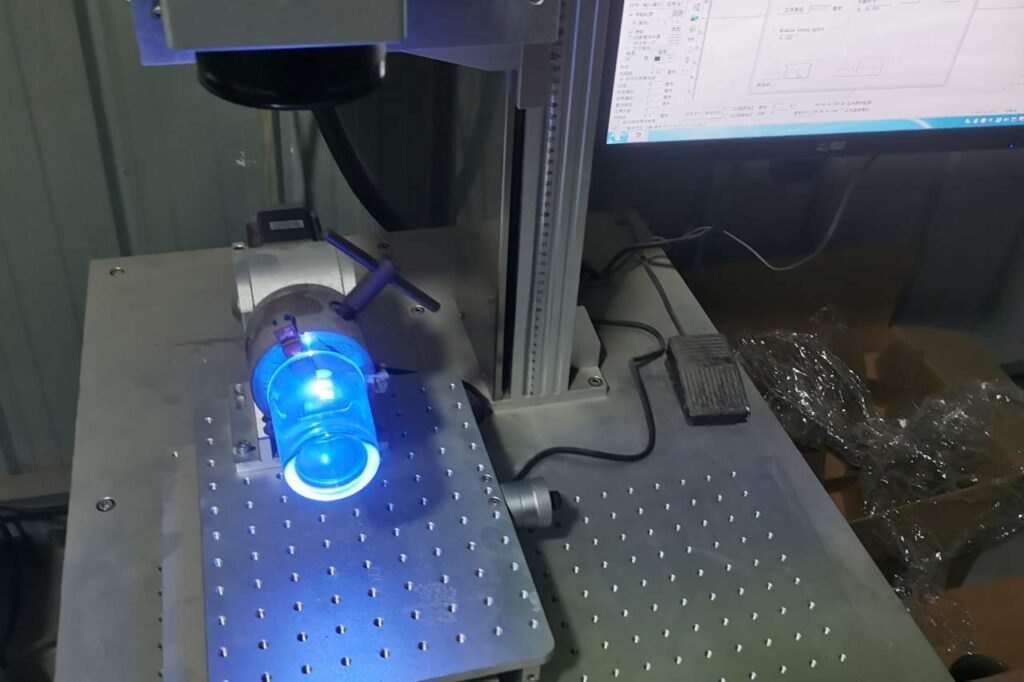
Engravings, Decals, and Embossing
For a more refined look, businesses can choose engravings, which provide a permanent, elegant design etched directly into the glass.
Decals offer colorful, detailed branding options that can include intricate designs or full-color logos. Embossing raises the design off the surface of the glass, adding texture and a unique tactile element to the glassware.
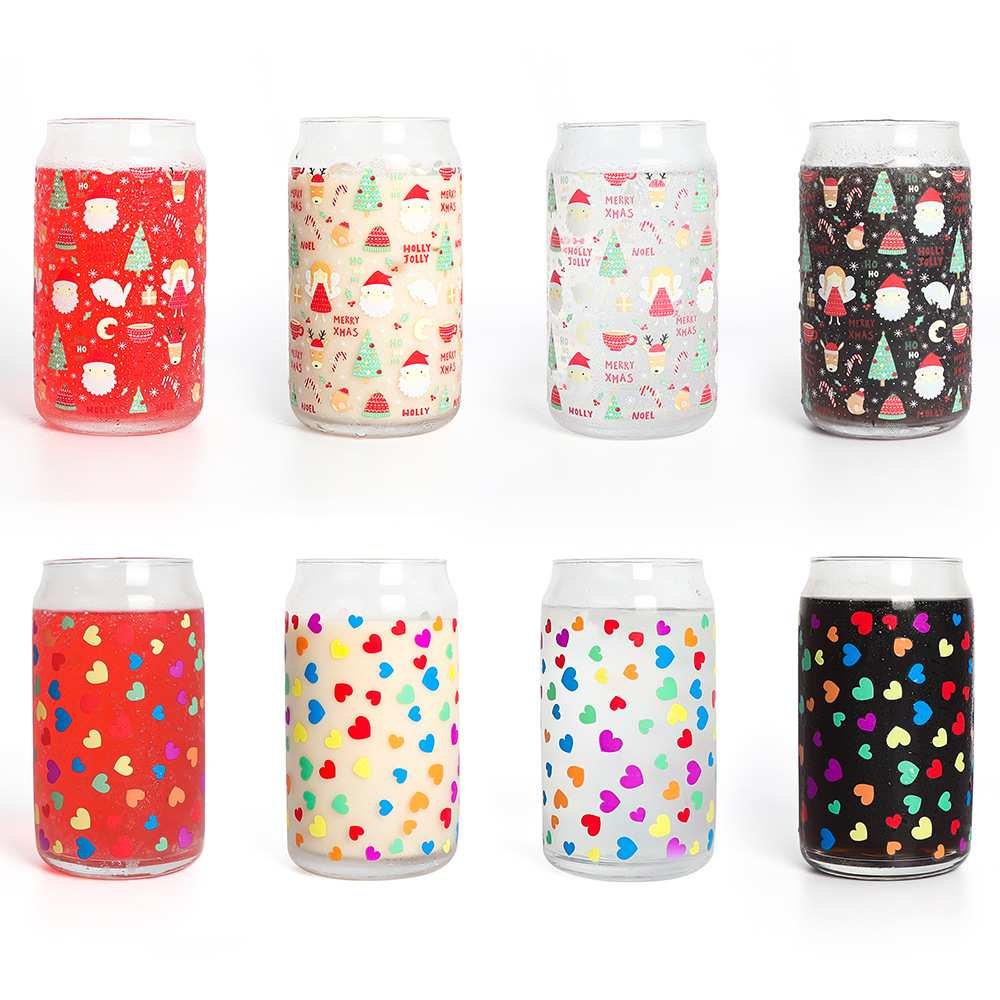
Different Color Options and Techniques
Glass cups can be customized with a variety of colors through techniques like painting. Painted glass allows for bold, vibrant hues, while etching adds a frosted, subtle design.
Color choices can be applied to the entire glass or specific areas, such as the rim or base, depending on the desired look.
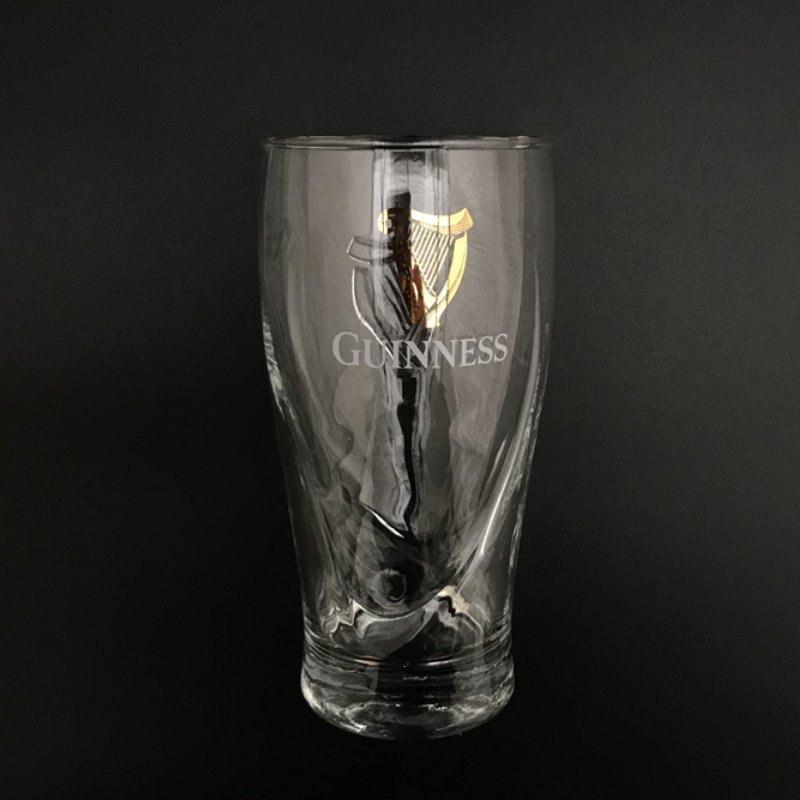
Different Glass Cup Shapes and Sizes
Glass cups come in a wide range of shapes and sizes, from tall tumblers to wide mugs. The shape of the glass impacts its usability—tall, slim glasses are great for cocktails, while wide mugs are ideal for hot drinks.
Custom shapes can make the glass stand out and better suit the drink it holds.
Order Process
DM makes ordering easy and efficient with a clear process from start to finish.
Submit Inquiry
Share your product requirements, specifications, and customization needs with our team.
Receive Quote
Get a detailed proposal and competitive pricing tailored to your needs.
Sample Approval
Review and approve product samples to ensure satisfaction before production.
Shipping
Products are packed securely and shipped to your destination on time.
Quality Inspection
Each product undergoes rigorous testing to meet international standards.
Production
Our team manufactures your products with strict quality control measures.
Contact Us
DM Glassware is a trusted B2B glassware supplier in China. We offer high-quality, customizable glassware for wholesalers and retailers worldwide.